After years of trial and error, experimentation, and rigorous testing, I’ve finally done it! Introducing a cable that surpasses the renowned Signature Series — a feat I’m sure you’ll appreciate, given the legacy and accolades the Signature Series has earned over the years.
As you know, my philosophy is: “If you’re going to do something, you do it right.” and creating something that could outperform the Signature Series required nothing less.
Hello to the Exquisite Ears. Please allow me to introduce...
Revolutionary Design for Ultimate Performance
Takshaka features a completely re-engineered “Eddie Twist” configuration, utilizing precise combinations of 24k gold, pure red OFHC copper, and pure silver (never plated) wires, all combined in 4 different size gauge strands. This redesign not only increases surface area of each conductor but also enhances the air dielectric, delivering unmatched clarity, detail and full-body musicality. This innovative design ensures every nuance of your music is captured and transmitted with absolute precision. Whether you're listening to the softest whispers or powerful crescendos, the Takshaka cables immerse you into the very heart of the performance. With approximately 40% more precious metal content than the Signature Series, I’ve fine-tuned the construction to extract every nuance of performance.
More Than Sound or Music – An Experience
With Takshaka, you’re not just hearing the music — you become part of the musical environment. The soundstage transforms, placing you not just near, but actually within the performance itself. It’s an experience where every instrument, every note, and every breath feels alive around you.
Enhanced Shielding and Power Efficiency
Designed for total signal integrity, the Takshaka interconnects feature double-shielding, while the Takshaka power cables are triple-shielded, blocking interference at every level. With a power cable between 9 and 10 gauge, the Takshaka eliminates the need for separate amplifier power solutions — one cable now powers everything, providing consistency and simplicity without compromise.
Looks That Match the Sound
Takshaka isn’t just about sound; I've also designed it to impress visually. The black exterior features an underlying layer of shimmering gold, giving the cable a subtle sparkle as you move past it. Gold and black carbon-fiber connectors complete the aesthetic, making the cables look as remarkable as they sound. Trust me when I say, pictures simply can not do justice to what this cable looks like in-person.
Handcrafted for You, One Cable at a Time
Like every cable from Snake River Audio, the Takshaka cables are handcrafted and custom-built, one at a time,
from the bare wire up, for each order. This meticulous approach ensures that every cable is not just a product, but a precision-engineered art masterpiece, tailored to perfection. By crafting every piece individually, we guarantee the highest level of quality control, allowing us to focus on precision, innovation, and attention to detail, culminating products tailored to true audiophiles who appreciate unmatched audio fidelity and a commitment to excellence. The result? A cable that performs flawlessly and provides a personalized listening experience like no other.
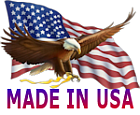
WHY CRYO?
Quick disclaimer: This is a very simplified explanation of the cryogenic process as it applies to electrical components of audio. We know and value the effects this process has on our products. But if you'd like a deeper more detailed explanation, you may have to consult a cryogenicist.
The raw materials used in ANY equipment, whether it's cables or tubes, or razor blades - all contain a harsh degree of residual stress. The process used to make wire itself is very stressful and straining on it's core materials. Then add to it the stresses of manufacturing that wire into a cable, soldering and twisting, etc. A cryogenic treatment relieves these stresses, and allows your equipment to perform above and beyond untreated models of the same. Resistance ratings are lowered and capacitance is improved.
The cryogenic process is well used in the audio world, from components to tubes, to cables, and with good reason. If you've ever seen how wire or some components are made, you can imagine what it's doing to that metal on a molecular level.
A very simplified analogy would be to think of two rows of numbers. The top row has numbers 1 to 5, while the second row goes from 6 to 10. Well, even through all the beating the metal takes, electrons try to stay loyal to the other atoms/molecules where they were connected before. But because everything has been twisted and reconfigured, the electrons might be trying to go from 1 to 7, then up to 2, back to 6, then over to 3, etc. Not a very efficient way to travel.
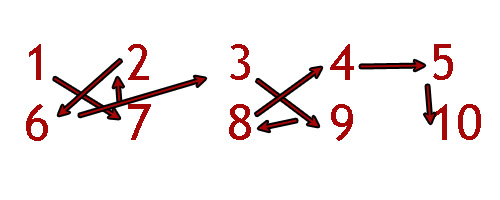
The cryogenic process utilizes liquid nitrogen, and very slowly lowers the temperature of the metals down to 320 degrees BELOW ZERO. It's actually so cold, that the electrons themselves practically quit moving. After being held at that temperature for a time to completely break any bonds those electrons had previously, the metals are then very slowly brought back up to normal temps. The effect that this has, is that when the electrons start moving again, they connect to the atoms/molecules closest and strongest to them, instead of wherever they were connected previously. Now, your electrons go straight from 1 to 2 to 3 to 4, etc. This results in lower capacitance and impedance. A much more efficient piece of conductive metal, which in audio, gives you better performance in your cables.
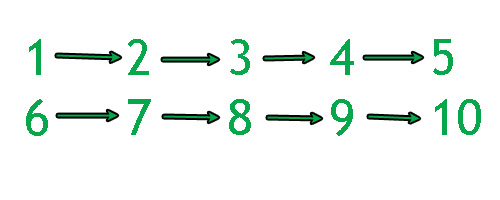
How does a cryo treated cable compare to an untreated model? Well, don't just take our word on this - feel free to search for yourself. There are many different accounts out there where a cryo treated cable performs better. The most common benefits attributed to cryogenically treatments are;
- Much more in-depth, focused three dimensional soundstaging
- Enhanced dynamic range
- Upper range notes are cleaner, more precise with less distortion
- Vocals are much more exact and clear
- Improved bass speed and articulation
DESIGN - EDDIE TWIST
The "Eddie Twist" (named after our beloved headphone-wearing snake mascot) method of our speaker and power cables takes advantage of, and maximizes the effects of two principles, dielectric and surface area or skin effect. By maximizing the surface area of our conductors, we greatly reduce the opposing eddy currents an A/C signal can create. But wait? How can you maximize surface area? There's only so much surface to be had, right? Well, we looked at traditional methods of wire stranding, and realized there was a simple way to do this. However, it's very time and resource consuming, and ends up utilizing more precious metal wiring.. which is likely why the mass-production cables aren't done this way. Take a look at the pictures below.
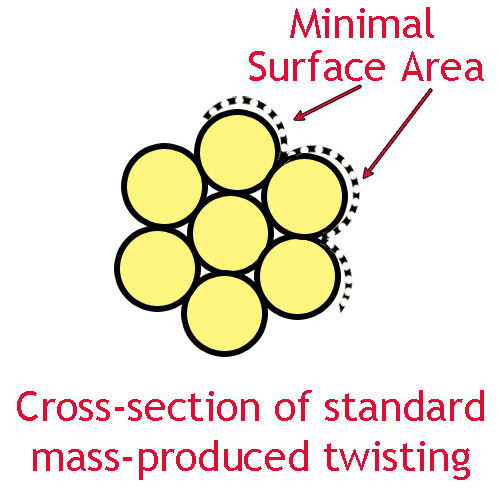
Most multiple strands cables are simply twisted all together at the same time. The end result is a very tightly woven group of conductors with much of their surface area actually touching each other. Our "Eddie Twist" method twists only one pair of conductors at a time. Then the pairs are twisted together, which gives you a cross-section that shows a much greater amount of surface area, touching nothing else.
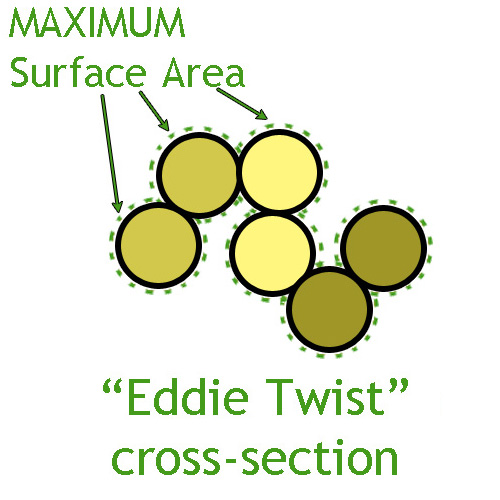
Now, let's talk about dielectric. To simplify, a dielectric is a non-conductive material that's used around and between your wires, to keep them from touching each other and shorting out. The problem, is that most non-conductive dielectric materials out there also absorb electrons, ie your music signal. Spread that dielectric all the way down the length of your cables, and that could be a problem. It's common knowledge that the absolute best dielectric possible.. is air. Just plain old air. If you could run bare wires from your amp to your speakers, with no dielectric at all, that would be the best scenario in regards to dielectics. However, that's really not feasible.
However, we designed a method to take advantage of our Eddie Twist configuration, and create a whopping 85%+ air dielectric in our cables. Think of a triangle, inside of a circle. Now make that circle slightly larger, and only two points of that triangle will ever be touching the circle at any one time. The rest of that triangle.. is open to the air.
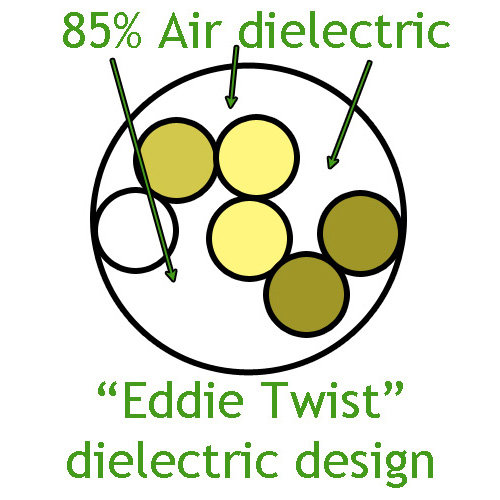
The principles of dielectrics and skin effect can be (and are) argued constantly on internet forums and chats. Our approach is simple. There's an old saying that says, "the proof is in the pudding". We simply invite you try our cables, and pit them against any other product out there. We are very confident in what we do. Over the years, we've had many skeptics of these principles, who have not only come back to us admitting that we're on to something.. but then backed it up by purchasing second, third, or fourth cables.
HOW LONG UNTIL I GET MY CABLES?
All of our cables are custom built, by hand, for each customer. We have no idea of what lengths or connectors people will need for all of the various types of cables, so we do not build up inventory in advance. On average, our build queue is about 5-6 business days out. Sometimes a little longer, sometimes a little shorter. Once a cable is completed, we prefer to put it on one of our curing systems for 200 hours before shipping out to the customer. This significantly reduces the amount of time for "burn in" on your system. This is preferred, but optional. The customer can choose to 'waive' the curing process.
You are always welcome to email us info@SnakeRiverAudio.com and inquire about our current build queue status. Typically, an order is ready to ship approximately two weeks or a little more from the date of the order.
After an order is placed, you will receive an email from us letting you know our current queue status, and when your order will be expected to be built. You can reply to us at that time whether you wish to waive the curing process, or have us complete it before shipping. You will receive another email after the cable is completed, and another when it has finished curing (if not waived). We also include your information with the tracking, so you will also get updates as the cable is en route to you.
30-DAY TRIAL PERIOD
We strongly believe in making your EARS happy! We also understand that it's not always easy to listen to our cables, and the difference they can make, in person before purchasing them. Auditioning products at a show, at one of our dealers, or even here in the demo room at our shop, is great.. but it's not going to match what you have in your own system, environment and setup. So, the absolute best audition is to buy our cables, try them out in your own home for 30 days. If you like what you hear, please shoot us an email telling us so! If you don't, return them within 30 days of receiving them for a full refund. Easy Peasy!! (disclaimer: returned cables will be inspected and tested for any damage, and refund will be minus shipping/handling costs and any credit card/paypal processing fees).
Obviously, to provide this type of guarantee, we are very confident in the quality and performance that our products can bring to your system. This comes from very rarely ever having a product returned. In fact, some recent research of our books showed that about 40% of our customers came back for even more of our cables! We love that feather in our cap!
FREE SHIPPING
Yep! It's true.. we offer free shipping on all orders! This just keeps getting better all the time, don't it?

IF THE LENGTH or design of the cable you are wanting is not in an easy dropdown, please email us info@SnakeRiverAudio.com